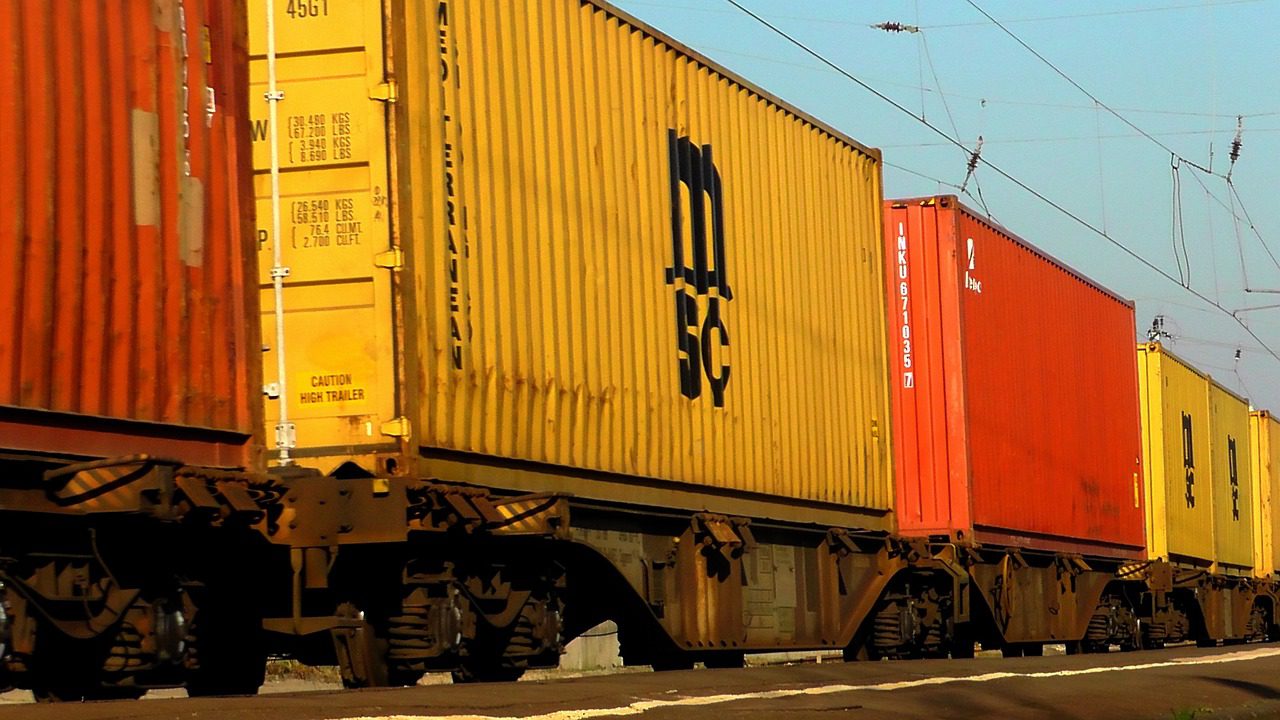
The global supply chain continues to be volatile in a post-covid world. Importers must face and overcome challenges that include fluctuating rates, fluctuating available space and equipment, significant delays, trucking shortages, and more. Most recently, at Dedola Global Logistics, we’ve helped our customers with issues involving the US rail supply chain due to union negotiations, potential strikes, and importers facing costly delays in shipping.
According to the Association of American Railroads, rail is part of an integrated network of trains, trucks, and barges that ship about 61 tons of goods in the US every year – making it an integral part of importing goods. Everything from lumber to coal to electronics rides the rails as it makes its way to the end user. Once your imported goods hit land in the US, the railroads play a key role in moving them where they need to be. Rail cars can hold 3 to 4 truckloads worth of weight. That means a single train could carry the amount of 300 trucks, according to Union Pacific.
Rail Freight is Facing Significant Challenges
Importers using rail need to stay on the lookout for emerging new challenges. Looming railroad strikes threaten to throw a kink into the domestic supply chain. A strike remains a possibility any time there’s news of breakdowns in talks between the union and management. A mid-November strike could impact goods arriving by the holidays. Dedola has been warning our customers of the possibility of a strike and helping them to make contingency plans to ensure that their cargo keeps moving. We help our customers to identify alternatives that meet shipping timelines and are cost-effective.
We’ve helped old, and new clients overcome rail freight adversities in recent months. One new client came to us because a week’s delay cost them a 10% fee by the buyer. The week’s delay was because of operational inefficiencies and mismanagement within the rail yard. The fee cut into the company’s profit margins. Dedola rescued their cargo from the railyard and streamlined future arrangements by bypassing rail and matching the exact costs of shipping to the final buyer.
We saw importers’ containers sitting for over a week in the railyards. The railyards unload the containers, pile them, and then don’t allow access to them. These piles are sometimes in restricted areas or not being put on chassis. The situation is exacerbated when railyards tell importers there is a chassis shortage. Other containers may move quickly out of the railyard depending on the service provider, freight forwarder, and their partners or connections at the rail port.
We’ve seen extreme cases where containers sit for up to 3 weeks at a high cost to the importer. Time lost equates to profits lost. In a consumer-driven nation, expedience in getting goods to consumers is critical. Dedola knows this, and our Operations team keeps our partners accountable and vetted by reliability and speed of service.
The Chicago railyard is the busiest in the nation and sometimes holds onto containers, while importers are not allowed to pick up their cargo. This is mainly because of mismanagement at the railyard, causing further congestion and chaos for importers. Dedola recommends that our clients terminate their cargo in Long Beach and truck it to the final destination.
Transloading
We’re also looking for solutions for our clients to avoid delays or having their cargo run the risk of getting caught in an avoidable roadblock. One way we’re helping our clients navigate the plethora of rail challenges is transloading. From Wikipedia, “Transloading is the process of transferring a shipment from one mode of transportation to another. It is most commonly employed when one mode cannot be used for the entire trip, such as when goods must be shipped internationally from one inland point to another.”
At DGL, we transload and ship via truck to ensure the cargo gets to the final destination on time. Sometimes, our customers have drop-dead deadlines, trade shows, or export deadlines. Transloading and shipping via truck eliminate the potential disruption the rail can bring to their supply chains.
The Economy Impacts the Inventory
Across the US, inventory has piled up in all facets of the supply chain, from ports to rail yards. We see warehouses completely full with shelves at retailers overstocked. Big-box to small and medium-sized retailers are putting significant portions of inventory on sale. The excess inventory is backed up from ports to warehouses and may not clear up until early 2023.
Conclusion
Dedola Global Logistics has over 46 years of experience ensuring importers overcome all possible obstacles along the supply chain. We’ve gone through every possible logistics and supply chain problem, and we have a blueprint for success no matter the crisis. Whether it’s the global supply chain plagued with shipping delays, work stoppages, equipment and space shortages, or peak season issues, we are a reliable partner that can help you fortify your business and protect your profits.
With volatility in the supply chain, now is the time to partner with a freight forwarder like Dedola. We’ve built our reputation on loyalty, long-lasting relationships, and dependability. We’ll work tirelessly to secure the space, equipment, and pricing you need while meeting time constraints. Our experienced staff will keep you informed, and you’ll have 24/7 access to our state-of-the-art customer portal TrakItPro. You can experience what we call the Dedola Difference. We deliver. Contact us today at (800) 561-0399 for a free consultation and a comprehensive quote.
READ: POPULAR BLOG – TrakItPRO – The Industry’s best real-time cargo visibility and tracking platform.